Continuous 3d Printing Using Paper Surface
March. 2017 – October. 2017, WPI. Independent Study Project
This is a team project with Michael Abadjiev.
- Testified that an FDM 3D printer can print continuously with a simple add-on device for the printing bed.
- Built a proof-of-concept example that can be used for automatic continuous 3D printing.
- Made the whole system simple and easy to install by utilizing the second print head controller circuit that is commonly found on most printers.
3D printing has huge popularity in prototyping. However, one issue is the need to removing the print manually after each print. In situation like school or maker place where people wait in queue to print, such problem gets amplified. This project aimed at giving 3D printer the ability to print 24/7 autonomously without human intervention with some simple modification. In the end, a prototype is built to demonstrate the solution we found is feasible.
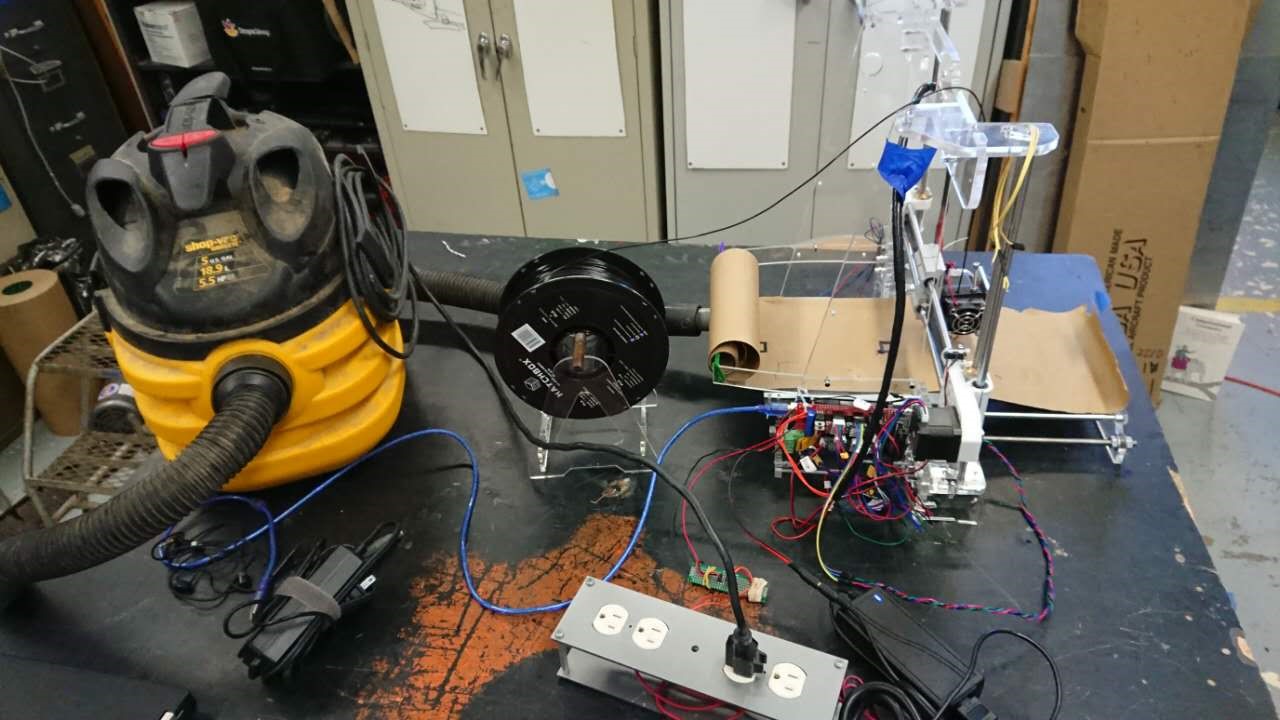
The full setup with Shop-Vac, paper roll, and printer with vacuum bed
Overall Setup for printing continuously
The main problem for printing continuously is the need for human to service the print bed (removing the print). Thus, the key feature in this project is the design that can auto-remove the print. Automatically removing the print is quite hard as prints very a lot. Some fragile print needs great care when removing off the bed without breaking them.
This project started with an interesting observation. While everyone is trying make a print stick to the print bed by applying Kapton tape, Carpenter tape (blue tape), glue stick, etc (flexible bed isn’t really a thing at that time). A simple piece of paper (example: regular printer paper) actually adhere well to the extruded plastic. It adhere so well in fact is is very had to remove that layer of paper from the print.
This good adhesion means paper is only good for one print, plus the fact that paper doesn’t stick onto print bed by itself makes people not interested about it. On the flip side, paper is cheap, very cheap, one sheet per print is not going to cost much at all.
Previously there are projects trying to solve the auto-print removal by preparing multiple rigid print bed (for example glass bed with blue Tape) and auto replacing them. This method requires a large storing area for all the finished prints as simply stacking rigid print bed onto pervious print will damage them.
By using paper as a auto-removed print bed, the storing becomes simple as the paper will not crush a print under it, paper is also fixable to be squashed into smaller area, and excess paper will also act as packaging. Further more, paper print bed could be stacked as sheets or rolls, giving great fixability and additional options.
Example of printer finished first print and move on to the second.
The next problem is holding down the paper non-adhesively. Tensioning paper from the sides would not work well. The pulling force to hold down the paper is perpendicular against the force from print that wants to peel up, which mean the pulling force will need to reach infinity as the paper gets pulled flat.
The solution is to use suction directly under the paper bed, and vacuum bed is the obvious solution. We have tried various design for this vacuum bed. By having high static force, low flowrate with small channel and many small holes on the vacuum bed is a bad option. As soon as the paper lifts a little, the vacuum is broken and the flow rate will not be able to hold it down. On the other hand, high flow rate and modest suction from shop-vacuum combined with a large channel and cutout vacuum bed seems to be the best choice.
The rest of the mechanism is simple, a pully at the front of the bed to pull prints off, and a relay connected to printer to control the vacuum. As a proof of concept, the setup works and performed quite well.
For future work, the vacuum system needs some fine tuning for the best efficiency. A cutter to cut-off the roll of paper when print is pulled off is optional but could be a nice improvement. Despite the vacuum design working quite well, is has the problem of large noise and high electricity bill. On the other hand, electrical-static suction design could be considered for low power and noise.